De vervoersketen loopt ‘just in time’ vast
De risico’s van productie zonder verspilling en opslag.
Een wereldwijd spektakel ontvouwde zich in maart 2021, toen het gigantische containerschip Ever Given dat vanuit Maleisië op weg was naar Rotterdam, zes dagen vast kwam te zitten in het Suezkanaal. Dit veroorzaakte de blokkade van 150 schepen, elke dag tegen een geschatte kostprijs van 1 miljard dollar (één dollar is 0,89 euro).
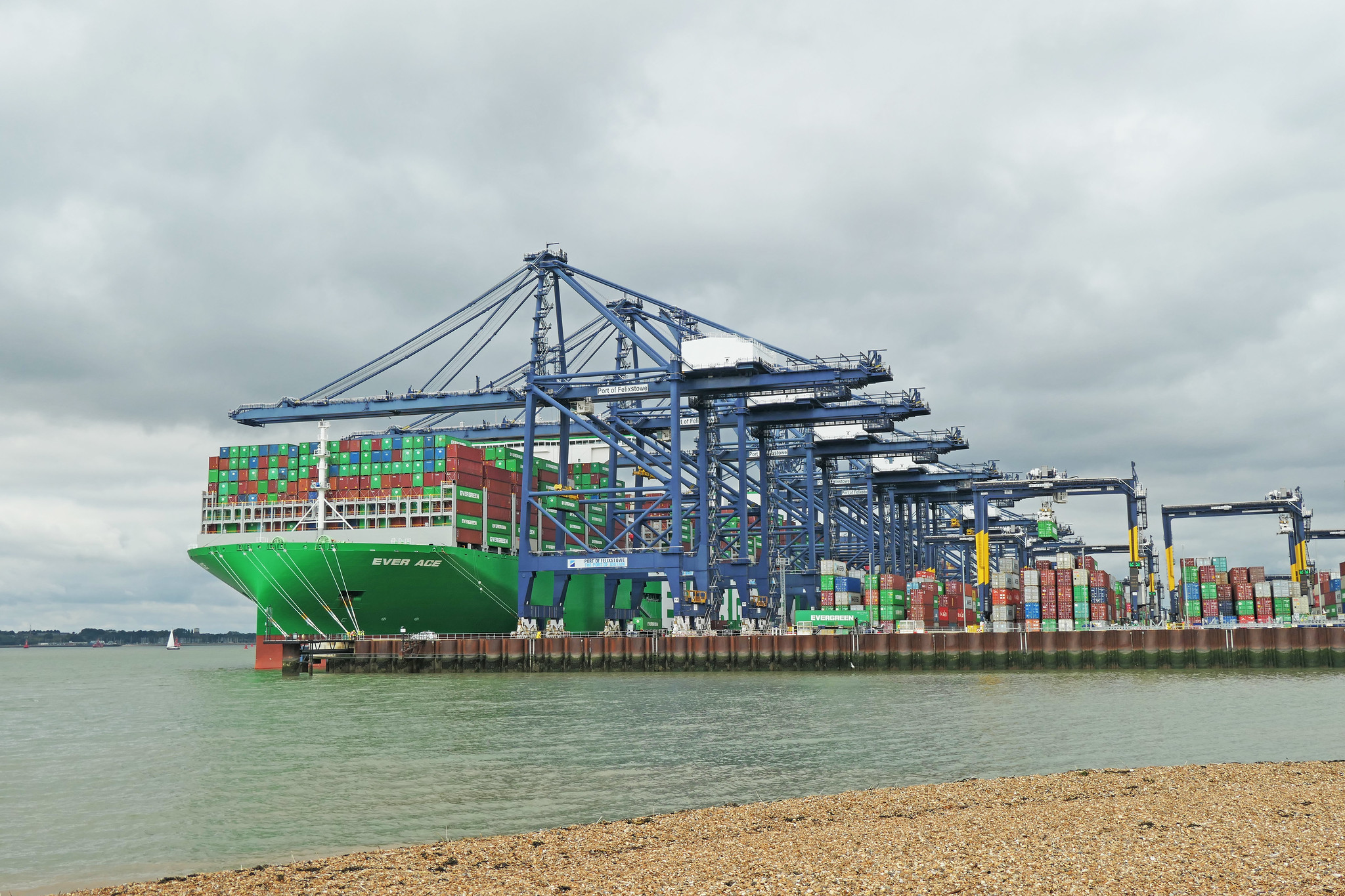
(Door Kim Moody (1) vertaling: solidariteit foto: de Ever Ace, nog groter containerschip dan Ever Given, Labor Notes, foto Amanda Slater, CC BY-SA 2.0)
Maar de Ever Given ramp was geen incident. Aan de andere kant van de wereld waren begin november zo’n 77 containerschepen op zee ‘gestrand’ buiten de havens van Los Angeles en Long Beach. Daarnaast moest een derde van de in het dok liggende schepen vijf dagen of langer wachten om te worden gelost.
Bureau Bloomberg verklaarde dat een wereldwijde crisis in de toeleveringsketen de logistiek managers dwong om de grenzen van hun opslagcapaciteit te benutten of op te rekken. Het Institute for Supply Chain Management meldde dat de productieactiviteit daalde, omdat de druk op de toeleveringsketen voor de Amerikaanse fabrikanten te groot was. Wat is er aan de hand?
Al voor de pandemie
De directe oorzaak van de crisis in de toeleveringsketen die in 2020 begon, was een sterke stijging van de consumentenbestedingen van duurzame goederen. Als gevolg van de Covid-19-beperkingen
bestelden mensen meer goederen voor thuis en maakten minder gebruik van winkels, theaters, bars en restaurants. Veel van die goederen kwamen uit het buitenland en moesten in ieder geval in het hele land worden bezorgd.
Het probleem begon echter niet met de pandemie. Het Amerikaanse vakblad Transport Topics meldde al in 2018 dat vrachtwagen- en spoorvervoerders moeilijkheden hadden om aan de vraag te voldoen.
De belangrijkste oorzaak van de crisis van de toeleveringsketen in 2021 in de Verenigde Staten is een al lang bestaand ’tekort’ aan werknemers om goederen te distribueren. Volgens de American Trucking Association is er een historisch hoog ’tekort’ van 80.000 chauffeurs. Dit zijn niet alleen vrachtwagenchauffeurs die door het virus zijn getroffen. Evenmin is dit ’tekort’ te wijten aan een gebrek aan mensen die vrachtwagens kunnen besturen. Zoals elke ’teamster’ kan vertellen, gaat het om de stagnerende lonen, de lange werktijden, de hoge stress en gezondheidsproblemen, waardoor werknemers vertrekken en werkzoekenden worden afgestoten. En dat was al lang het geval, voordat de pandemie toesloeg.
Stiptheidsschema’s
Magazijnmedewerkers die ook te maken hadden met stagnerende lonen en slechte arbeidsomstandigheden, waren om dezelfde redenen relatief schaars. De recente loonsverhogingen, het gevolg van deze arbeidstekorten en het veelvuldig vertrek, zijn te weinig en te laat.
Om het nog erger te maken, hebben de grote spoorwegvervoerders die het continent bestrijken de afgelopen jaren hun personeelsbestand teruggebracht met behulp van hun versie van ‘just-in-time lean’ productie’: stiptheid vervoerschema’s in ‘slanke productie’. Als gevolg hiervan daalde het aantal werknemers op de goederentreinen van klasse I van 170.000 in 2017 tot 135.000 in 2020, terwijl het goederenvervoer per spoor tussen 2010 en 2019 met 40 procent in gewicht en 37 procent in dollarwaarde toenam.
De organisatie Railroad Workers United wijst erop dat de stiptheidsschema’s bijdroegen aan de crisis in de toeleveringsketen. Door ‘zo nodig’ de uitrusting van treinwagons te vereenvoudigen en de overbelasting van de havens, terminals en het uitgeputte treinpersoneel terug te dringen.
Een gebrek in de toeleveringsketens aan onder anderen vrachtwagenchauffeurs, spoorwegarbeiders en magazijnmedewerkers leidde tot overbelaste havens, vastgelopen geloste schepen en overvolle magazijnen. Met als gevolg lege schappen en hogere prijzen. Kortom, zo stelde een topmanager vast: het transport zit vol verstoringen, er is een gebrek aan vrachtwagenchauffeurs en de werving van personeel voor magazijn- en transportbanen is problematisch.
Toen begin 2020 de pandemie toesloeg, stegen de levertijden van productie- en constructieleveranciers in de Verenigde Staten met 30 procent. Dat wil zeggen: een levering die voorheen twee dagen duurde liep op tot twee en een halve dag. Tegen het einde van het jaar daalde het iets, maar halverwege 2021 schoten ze weer met meer dan twee derde omhoog.

Uit: Lean Management Journal, oktober 2012.
‘Net-op-tijd’
Wat deze ongekende verstoring van de toeleveringsketen zo hard en snel deed toeslaan, was de snelheid waarmee een enkele storing in de productie of het transport van goederen door een tekort aan arbeidskrachten of door logistieke obstakels de leveringen over de hele wereld kan verstoren.
Als tegenwoordig onderdelen aan een fabriek worden geleverd of huizen verkocht, gebeurt dit op een just-in-time basis – ‘net op tijd’. Een onderdeel dat bijvoorbeeld door een autofabrikant bij een leverancier is besteld, wordt verondersteld aan te komen op de assemblagelijn in plaats van in een voorraad te worden opgeslagen. Dit strak geregelde uurwerk is ontworpen om goederen en geld alsmaar in beweging te houden. Maar zodra een schakel in de ketting breekt, vastloopt of overbelast raakt, is het effect onmiddellijk, diep en algemeen voelbaar. Just-in-time levering veroorzaakt zo zijn eigen ondergang.
‘Net op tijd’ was het geesteskind van Taiichi Ohno, een ingenieur bij Toyota Motors in de jaren vijftig. Als onderdeel van de ‘slanke productie’ omschreef hij just-in-time levering als een manier om de winst te vergroten door ‘verspilling’ in de vorm van voorraden, extra werknemers en productietijd uit te schakelen. In plaats van tijd, arbeid en geld te besteden aan de opslag van onderdelen langs de assemblagelijn of in een magazijn (zoals fabrikanten dat al tientallen jaren deden) was het idee van Ohno dat leveranciers deze konden leveren zodra ze nodig waren, waardoor voorraden werden opgeheven.
Dit betekende het temmen van Japanse vakbonden en een enorme verhoging van het werktempo. Jaren later haalde Ohno herinneringen op: Als ik tegenover de (militante) vakbond van Japan National Railways of een Amerikaanse vakbond had gestaan, was ik misschien vermoord.
Just-in-time versnelling
Vanaf de introductie van de slanke productie en just-in-time in de auto-industrie in het Westen in de jaren tachtig, verspreidden deze methoden zich naar elk type productie of diensten, het transport en de detailhandel.
Grote retailers als Walmart en Amazon en producenten als Ford en General Motors legden dit beleid aan de toeleveringsketen op. Elke leverancier, groot of klein, werd geacht producten just-in-time aan de volgende koper te leveren. In het geval van Amazon of Target betekent dit de minimalisering van de voorraden van goederen op basis van de verwachte vraag naar dat product met behulp van een digitale analyse.
Amazon verplaatst goederen zo snel door zijn systeem dat de betaling van een gekocht product al plaatsvindt, voordat het bedrijf zelf zijn leverancier betaalt.
De kwestie was kosten en arbeid verminderen door voorraden te verminderen. En inderdaad, de verhouding tussen voorraden en verkoop voor niet-agrarische bedrijven in de Verenigde Staten daalde in de periode 1980-2020 met 35 procent. Samen met andere besparingen op arbeid hielp dit de Amerikaanse binnenlandse, niet-financiële bedrijfswinsten met 40 procent te doen stijgen met 1,8 biljoen dollar in 2010-2020, ondanks de relatief trage economische groei.
Net opslaan, maar verplaatsen
Om het tempo in de toeleveringsketen te verhogen, werd het magazijn van de 21ste eeuw omgevormd van een opslagplaats in een ‘bewegingsplaats’: goederen gaan de ene deur in en de andere zo snel mogelijk uit. Hoewel er meer magazijnen en magazijnmedewerkers zijn dan twintig jaar geleden, wordt weinig van deze groei van ruimte en personeel besteed aan opslag. Dus toen de pandemie toesloeg en de consumentenvraag steeg, waren er geen voorraden aan te spreken. In plaats daarvan gingen er meer goederen het land in en door. En zonder voldoende arbeiders om ze snel genoeg te verplaatsen, stapelden de zaken zich op en liepen de files vast. Alle ‘big data’ en digitale coördinatie van toeleveringsketens konden een gebrek aan werknemers niet overwinnen.
Snelheid brengt grotere risico’s met zich mee. Overstromingen, stroomuitval, computerstoringen, slechter wordende wegen, arbeidsconflicten, of zoals we nu hebben gezien, pandemieën en handelsproblemen kunnen een just-in-time systeem tot stilstand brengen, omdat het systeem geen speling kent. Lage voorraden vergroten het risico op verstoring, terwijl snelheid de ontwrichting op en neer doet gaan als ‘rimpels’ of ‘sneeuwbaleffecten’.
Verstoringen hebben niet alleen een snelle invloed op de leveringen, maar ook op de financiën van een bedrijf. Zo bleek uit een onderzoek onder 397 Amerikaanse bedrijven tussen 2005 en 2014 dat een enkele verstoring van de toeleveringsketen van welke aard dan ook een gemiddelde omzetdaling van 4,82 procent veroorzaakte. Daarbij daalde het bedrijfsresultaat met 26,5 procent en het rendement op investeringen met 12,7 procent. Een situatie die voortduurde tot drie maanden na het incident. Aanvallers let op.
Risico, veerkracht, tegenmacht

Zich bewust van alle potentiële problemen, hebben hedendaagse ‘managers vervoersketen’ gedebatteerd over ‘risico’ versus ‘veerkracht’. Veerkracht, in de betekenis van ‘voldoende speling’, in het systeem aanbrengen om verstoringen te minimaliseren of snel te herstellen. Dus, waar nodig; meer voorraden, meerdere leveranciers, hogere kosten en vooral meer werknemers en mogelijk minder winst.
Decennia deregulering, privatisering en markt aanbidding, gericht op winstmaximalisatie, hebben de samenleving kwetsbaar gemaakt voor de ongebreidelde kracht van just-in-time toeleveringsketens. Gelijktijdig ontbreken de politieke middelen om het beest te temmen. Verzwakte vakbonden en een beleid van klassensamenwerking ontnamen de arbeiders ieder vermogen om weerstand te bieden op de plaats waar die nodig was in de toeleveringsketen: de arbeidsplaats. Waar dan ook, fabriek, magazijn, vrachtwagen, trein, haven, computerscherm of een winkel.
Ongeacht de mate van automatisering 0f digitale controle in de toeleveringsketen zijn productie en verplaatsing van goederen en levering van diensten afhankelijk van werknemers. In totaal gaat het om miljoenen, alleen al in de Amerikaanse infrastructuur en transport. Uiteindelijk wordt de snelheid van just-in-time levering gevormd door intensivering en versnelling van de arbeid. Op zichzelf kunnen ‘big data’ niets verplaatsen.
De ‘veerkracht’, door managers tientallen jaren uitgehold door steeds weer de productie en het werktempo op te jagen, is in de eerste plaats te vinden in voldoende arbeidskrachten om het werk in een gezond tempo te doen. Om de productie en het verkeer van goederen en diensten op een gezonde basis te organiseren, is het nodig te strijden voor fatsoenlijke arbeidsomstandigheden in de hele toeleveringsketen.
De opbouw van sterke vakbonden, de verbetering van de leef- en arbeidssituatie, de verkorting van de arbeidsduur en de verhoging van de lonen, vormen noodzakelijke voorwaarden om de crisis in de toeleveringsketen tegen te gaan. Personeelstekorten zullen dan tot het verleden horen en er zal een klap worden toegebracht aan de schandalige ongelijkheid van vandaag.
(1) Kim Moody is één van de oprichters van Labor Notes, 1970 – labornotes.org. Zijn artikel verscheen 6 december 2021 in Labor Notes, titel: The Supply Chain Disruption Arrives ‘Just in Time’. Vertaling/bewerking Roland Siebe.